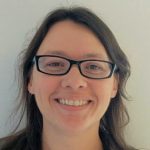
One of the most significant opportunities available to factory leaders is the convergence of operational and information technologies (OT and IT) on the plant floor.
Yet, adoption of IT in Canadian factories remains slow, a fact due – at least in part – to several misconceptions and fears about Ethernet-based networks and the impact they will have on the factory floor.
Related: Are Canadian manufacturers ready for Industry 4.0? Sadly, the answer is no.
I understand why the introduction of IT into your industrial environment sounds frightening.
An IT network increases your vulnerability to cyberattacks, right?
Doesn’t it makes floor management more complex?
Won’t floor operations lose control of production once an IT network is in place?
With all these myths floating around about what actually happens when an IT network is introduced to the factory floor, I decided to settle the issue once and for all.
The truth is that an Ethernet network does not increase your vulnerability to cyberattacks, does not make floor management more complex, and does not surrender control of your factory to your IT colleagues.
In fact, the right IT network will not only make your factory more secure, more efficient, and give you more control – it will make your job easier.
Myth #1: An IT network makes my factory floor vulnerable to cyberattacks
While it is true that legacy industrial controls are vulnerable to outside threats once connected to the internet, the myth that IT makes your factory floor vulnerable is false.
The reality is that this vulnerability exists whether an IT network is in place or not. The industrial automation and control systems (IACS) on your factory floor are already a security risk. Your machines were never built to protect against sophisticated threats.
It is also true that as more of your industrial control systems are connected to the industrial internet, more of these vulnerable machines become a target for hackers. The Dragonfly malware program targeted more than 100 IACS in 2014. Attacks on industrial networks continue to rise each year. It is vital that these legacy control systems, which can be 20 years old or older, be secured against today’s cyber threats.
Related: Industrial Control Systems Cybersecurity Guide | Manufacturers, don’t choose your own cybersecurity adventure
But concern over vulnerabilities is not a reason to avoid an IT network on your factory floor. Why? Because the right IT network – a network built for digital applications with security in mind – mitigates these threats and improves your floor’s security posture.
A secure IT network intelligently and logically monitors traffic, giving your IT team end-to-end visibility of possible threats. The result? You rest easy knowing your machines are protected against attacks that could result in production downtime, physical machine damage, or Intellectual Property theft.
Myth #2: An Ethernet network will complicate floor management
A common misconception about IT on the factory floor is that an Ethernet network, be it wired or wireless, makes production management more complex and time-consuming. But in truth, the introduction of an IT network simplifies equipment management by providing a single ‘pane of glass’ view for floor managers.
Imagine this. Instead of walking the floor to manually record data from each machine, you simply open an application on your tablet and see – in real-time – how each machine is performing. In addition to performance, the application displays analyzed historical data and provides alerts for machines that may require maintenance or are underperforming. All because your industrial control systems are connected to a common IT network that collects this data in. One. Space.
You get hours back in your day, freeing you for more strategic priorities such as improving OEE or identifying areas for improved utilization. An IT network also signals the end of the days of the closed-loop legacy network, where information wasn’t shared between systems. Advancements in protocols such as Time Sensitive Networking (TSN) are ensuring the future of factory floor management will be easier and more intelligent than ever before.
Myth #3: I will lose control of the factory floor to IT
This is a concern we hear all the time from floor leaders hesitant to deploy an IT network in their factory. If you feel this way, know you are not alone. Converged IT and OT networks is an emerging reality for many manufacturers, and managing these networks requires trust and open communication from both teams.
But there’s a secret you should know: IT doesn’t want to manage your factory floor.
Your company’s IT team is plenty busy with user and device management, network administration, security updates and patches, and many other day-to-day tasks. The last thing they want to do is add management of the factory environment – and all those machines – to that list. But what IT will want is to work in tandem to ensure your factory is secure and up-to-date. So while this means having to schedule downtime for when it’s convenient to perform network upgrades and repair machinery, it also means you have greater visibility and insight into production – without giving up control.
If you want to know more about how IT and OT can work together, download this free whitepaper.