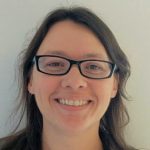
Unplanned downtime can cost manufacturers up to $20,000 a minute. That’s $333 for every second production is halted, a potentially-crippling amount for small and mid-size manufacturers who are already feeling the effects of higher energy costs and slim margins.
But there’s good news. Unplanned downtime can be reduced – eliminated, even – with the right combination of technology and expertise. Here’s how.
Eliminating downtime starts with troubleshooting problems on your factory floor effectively. The best way to do this is to provide your machinists and automation experts with the data they need to find a solution. A secure IT network that can collect and analyze machine data is the first step to delivering this information.
Related: New Network Saves Factory $1M in the First Year | Struggling with How to Close your Factory’s Talent Gap? Try Collaboration.
Armed with data on machine health and historical performance, provided over the network and delivered on a tablet device, your experts on the floor can better locate issues and remedy problems as they arise. Increasingly, virtual reality and video solutions are also being used to connect remote machine experts, in real-time, to assist with troubleshooting and repairs.
https://www.youtube.com/watch?v=hlvEjABsbZ8
The best part about all of these technologies – Wi-Fi connected tablets and other devices, virtual reality, and video – is that all are made possible with that single, secure IT network I mentioned above. And despite what you may think, a network doesn’t need to be expensive. Cisco Meraki, for example, is an easy-to-use, easy-to-manage and affordable networking option for most businesses.
The choice is yours. Make unplanned downtime a problem of your past by providing employees with the right tools, data, and expertise to troubleshoot more effectively. Then tell us your story in the comments below.