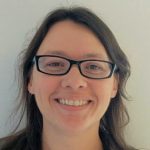
Part Two: Discussing the Industrial Internet of Things with David McPhail, CEO, MEMEX
3 min read
Cyber-physical systems are dramatically changing the manufacturing industry. MEMEX Inc., a Canadian software and hardware provider, is helping making the factory of the future a reality for manufacturers around the world.
In part two of our conversation with David McPhail, CEO of MEMEX, we talk about how to simplify the Industrial Internet of Things (IIoT), the results MEMEX customers are experiencing with IIoT solutions and his advice for Canadian manufacturers.
Read part one of our conversation here.
Jennifer Rideout: The Industrial Internet of Things (IIoT) is still a confusing subject for many manufacturers. What are your thoughts on the IIoT and how do you explain the concept to your customers?
David McPhail, CEO, MEMEX: We recognized long ago that in order for our customers to understand and benefit from the adoption of IIoT technology and the associated business outcomes, we had to boil the perceived complexity of IIoT down to a few digestible pieces.
For the promise of IIoT to be real, there must be data. This data must be collected securely from all manufacturing assets, regardless of their type and age, utilizing a robust and secure connectivity layer consisting of either machine side hardware devices or available software protocols such as MTConnect or OPC.
This data is collected in real-time and easily displayed and reported to the entire operational management team. The use of this data must lead to tangible business outcomes, with a repeatable and demonstrable value equation or ROI.
In our case, MERLIN calculates Overall Equipment Effectiveness (OEE), the most important efficiency metric in manufacturing today.
JR: I’d like to make the IIoT real for our readers. Give me a few examples of how your customers are using MERLIN to produce tangible, measurable business outcomes.
DM: Mazak is one of the best example that comes to mind. Together with adopting MERLIN, Mazak deployed a series of 60-inch display monitors across their plant to establish a visual performance benchmark, and related training protocols, that could easily expand across their massive machine tool manufacturing plant.
For the first time, Mazak’s top management and operational teams had access to actionable reports. This led to a host of immediate valuable improvements. Their adoption of MERLIN afforded them a 42% productivity increase within the first six months, along with reducing operator overtime by 100 hours/month. Another benefit was the return of 400 hours/month of previously outsourced work.
This project also resulted in the development of SmartBox, a platform that allows for an easy and secure entrance into the IIoT for manufacturers.
JR: Thanks for your time David, I have one last question. What advice do you have for manufacturers who want to adopt IIoT solutions, but aren’t sure where to start (or how)?
DM: In any decision where there is new ground to be broken, such as the adoption of IIoT-centric technology in manufacturing, the first questions should be WHY? Unfortunately too many companies focus on the HOW first, and that is where the confusion starts, in my opinion.
When a company ignores the “why should we do this” question in favor of the “how do we do this” question, the anticipated IIoT-centric business outcome has been relegated to the second-most important piece of information. The HOW is where all the technical issues are addressed. These can include both technical specification-type details, as well as internal change management-type issues that, although important in their own right, unfortunately do not assist the decision maker in determining the net effect that an IIoT project can have on the company’s bottom line.
The WHY is the first question that should be answered, as this will accurately paint the picture of the anticipated investment in IIoT (the risk), as well as the anticipated business outcome (the reward). Only once this piece of important information, the business outcome (the WHY), is understood by decision makers, and the project “greenlighted,” is the HOW relevant.
We have many case studies of manufacturers that have blazed the IIoT trail for others to follow. The number one item to be learned from their IIoT implementation is the actual ROI received for the efforts expended.
My advice: start with the ROI value and timeline and determine if the project cost (the investment) is worth the price of success.
My thanks to David for taking the time to share his thoughts. If you’re ready to start your journey on the IIoT, download our free eBook.