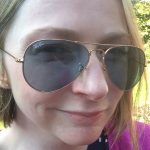
From Cyber-security to AR on the Factory Floor: 5 Predictions for UKI Manufacturing in 2017
3 min read
Brexit, Brand vs Retailer wars and the aftermath of the automotive emissions scandal, 2016 was certainly tumultuous year for UKI manufacturing.
As we head even further into the unknown, here are five trends we expect to see make their mark in 2017:
#1 – Security will become a key priority
Following a number of high profile industry cyber-attacks in 2016, including ThyssenKrupp and Hangzhou Xiongmai Technology Co Ltd, which made parts for devices that were targeted in a major global hacking attack, this is the year manufacturers will get serious about security. And with good reason – manufacturing is now one of the top three industries targeted in cyberespionage, the second is percentage of spam in email and the third is spear-phishing. The number of attacks on legacy industrial control systems has also sharply increased as they are increasingly connected to corporate networks and the internet.
Manufacturers need to get their houses (well, factories) in order ahead of regulatory changes, notably the EU GDPR, which will force industrial businesses to disclose cyber-attacks, even where no customer data has been compromised.
#2 – Machines will get smarter
As the fourth industrial revolution gather momentum, automation, a game-changer on introduction in the 1960s, will no longer be enough. Artificial intelligence will become commonplace on the plant floor, with sensors routinely deployed to spot defects easily missed by the human eye, but with the potential to create major quality issues down the line and rack up significant costs in repairs, recalls and lost business.
Machines will not only perform ever-more sophisticated tasks, but machine learning will drive quality and productivity improvement across industry. Smarter machines will also offer a real solution to many of the problems created by an ageing workforce and the impact of the living wage. They won’t replace people, but they will free people from monotony, to focus on more rewarding tasks.
#3 – Focus on workforce experience
Manufacturing is going digital, but what about the workforce? The industrial sector is definitely seen as a laggard in terms of mobility and, as a result work-life balance, with many of the young talent employers so desperately want to attract frustrated by the need to be in the office or on the plant floor to carry out critical tasks. Not to mention the experienced older workforce who are frequently juggling family commitments and/or travelling between sites while the inbox overflows.
This is a status quo born partly from tradition but mainly through a reliance on legacy technology and 3D business applications that simply weren’t designed to be accessed remotely. However, collaboration technologies are increasingly solving many of these issues, with remote team working facilitated more and more and start-ups such as Cisco partner ebb3 designing innovative solutions that allow CAM and CAD graphics to be accessed from anywhere, a huge boost for those previously shackled to the desktop by necessity.
#4 – Augmented Reality (AR) will go mainstream
2016 may have been the year of Pokemon Go, but 2017 will see AR deployed widely in an industrial environment, where it has the potential to positively impact on productivity and costs. In an industry where multiple sites are the norm and facilities are frequently vast in size, getting to a machine to investigate an alert or carry out routine maintenance is currently a much bigger job than you might expect. Despite downtime striking fear into manufacturers everywhere, it’s surprisingly common for a critical machine to be out of action while an expert is flown in to diagnose or fix a fault.
With AR, combined with the use of wayfinding and collaboration technology to capture the machine’s readings and locate it, remote experts can diagnose the problem quickly and simply and assist a local technician to fix it. Productivity maintained, no travel costs and waiting around. Far more exciting than chasing cartoon characters around a precinct.
#5 – The value chain will collaborate more than ever before
The industrial internet of things (IIoT) works on the basis that all things can connect easily. Yet the manufacturing environment is full of connectivity and communication protocols that are not interconnected and often not interoperable. Convergence and interoperability are critical if Industry 4.0 is to live up to (huge) expectations.
2016 saw a breakthrough on the technology front, with a group of leading industrial technology vendors, including Cisco, General Electric, National Instruments & Schneider Electric, committing to developing products using the same communications protocol. During the coming year, there will be more collaboration between links in the value chain, including competitors – necessary to realise the potential of digitisation.
Of course, not all of these trends will affect each manufacturing business in equal measure. How many will drive change in your business this year?
Next steps:
- Watch our video on how the factory of the future is already here
- Check out the first in our Manufacturing Cyber-security blog series
- Sign up to the Cisco UK & Ireland blog to make sure you don’t miss the next in the series
- Visit our web page to read more about Cisco solutions for manufacturers