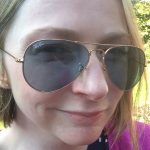
Supply and demand – a simple, evenly balanced equation. Said nobody involved in manufacturing, and certainly not in the UK and Ireland right now as sterling proves about as reliable as the weather. After a week that saw a very public spat between a major retailer and manufacturer over the sharply rising costs of producing some of the nation’s best-loved branded consumer products, it seems clear we should brace ourselves for further supply chain volatility.
UK exporters are, of course, rubbing their hands with glee at the prospect of an exceptionally favourable exchange rate. Unless they happen to source many of their raw materials from outside of the UK, in which case the benefit is tempered. For manufacturers in Ireland who export to the UK (Ireland’s second largest import partner), the situation has less welcome implications.
UK manufacturing output continues to soar, against the consensus of opinion immediately post-Brexit. Yet with a timescale now placed on the UK’s exit from the EU, the supply chain planning process is becoming more and more of a gamble. Rollercoaster exchange rates make it extremely difficult to accurately price raw materials, yet retailers – and end-users – are understandably reticent to accept predictive price increases.
Productivity, productivity, productivity
Given that the likelihood of an extended period of exchange rate volatility, what can manufacturers do to keep production lines – and trading relationships – rolling?
It’s certainly not new and it’s cited too often to be clever, but productivity really is the secret weapon in the manufacturing box of tricks when economic factors are conspiring against you.
Reporting better-than-exported full year results this week, luxury confectioner Hotel Chocolat cited productivity – alongside UK-located production facilities – as being at the heart of its strategy to combat increasing supply costs (as reported in the Evening Standard).
That old chestnut
But surely manufacturers are constantly looking to drive productivity improvements, I hear you ask incredulously? That is indeed true, however the counter argument is that IoT technology is now stable enough, and widespread enough, for manufacturers to connect their machines, to harness the big data that’s swirling around by the terabyte and generate genuinely insightful analytics…
Analytics that will show up where energy is being wasted, where production lines are running at less than capacity, where machines are out of use or even better – when it’s going to happen.
And how about cutting down on site visits by using HD video and augmented reality to allow remote experts to complete a diagnosis based on the data already generated and processed by your connected plant floor?
The incremental benefits might not neutralise the effects of the plummeting pound, but they may well be enough to offset at least some of the fluctuations.
Never a better time
Without wanting to sound like a stuck record, we all seem to generally agree that IoT – if the security issues are addressed and the technology is stable and does not create downtime – is a good thing. Yet we’re far from fully seeing the benefits in an industrial setting.
So when will there be a better time to bite the bullet and use the UK’s greatest innovation of recent times (the internet) to its full potential and make our factories as smart as our great R&D talent and as lean as our six-sigma gurus?
Next steps:
- Watch our video on how a connected factory gives you more control over your business
- Find out how IoT powered a factory upgrade for Cisco customer Daimler Trucks
- Sign up to the Cisco UK & Ireland blog to make sure you don’t miss the next in the series
- Visit our IoT page to read more about Cisco solutions for manufacturers