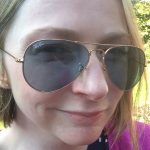
Supply chain security is rising up the boardroom agenda among global manufacturers, as incidences of theft, fraud and counterfeiting and even infiltration by cyber-attackers become more frequent, more widespread and increasingly newsworthy.
And the cost is staggering. Businesses lose an estimated $22.6bn globally each year due to cargo theft, and the price paid by manufacturers impacted by other supply chain risks also adds up:
The horsemeat scandal of 2013, which saw major retail brands and manufacturers forced to withdraw millions of meat-based products after supply chain fraud was discovered, wiped a reported £300m off the share price of one major brand.
In 2016, a China-based manufacturer recalled some of its products sold in the US after security researchers identified it had made parts for devices that were targeted in a major IoT global hacking attack credited with a widespread takedown of the internet.
$22.6bn
Value of annual global losses due to cargo theft
(source: BSI, 2016)
It’s no surprise therefore that manufacturers are looking for reassurance that each item used on their production lines has a genuine and traceable provenance, and that products dispatched for onward supply are not interfered with. However, sourcing and then tracking of components is a hard-enough job in itself. What can supply chain managers do if their suppliers are unable or unwilling to provide a cast-iron audit trail?
Consumers, too, are demanding more and more information about the history of their purchases. IoT-based initiatives such as the Safety for Food platform, for which Cisco supplied the behind-the-scenes connectivity for our customer Barilla Pasta, have made progress in providing this visibility. In this example, purchasers can scan a QR code on packaging to access details on the production batch and supply chain journey. Yet this level of detail is not routinely available.
Enter, the world of blockchain. In theory, at least, blockchain provides a panacea to the recognised headache of supply chain security. Not only does it have the potential to track product journeys to the most granular level, providing visibility to all who need it, but also it offers opportunities to automate many largely manual processes, reducing the administrative bill into the bargain.
But just how would blockchain work in practice across the supply chain?
How it works
A blockchain is essentially a database stored in multiple locations that maintains continually increasing records, or ‘blocks’ which are timestamped and linked to the previous block in a way that cannot be undone.
In the context of the supply chain, goods would be registered on a global ledger as transactions, with pertinent information such as the cost, geographic location and date, as well as the parties involved in production and transportation.
This information would be available securely to verified supply chain partners. It, or a version of it, could even be made available to the general public where the appetite to understand the exact history of goods is present – for example, where serious food allergies exist, or purchases are influenced by consumers’ religion or beliefs.
Current security efforts such as control towers and track-and-trace at shipment level offer limited protection from the determined efforts of pirates and counterfeiters who plague the global supply chain, despite the best efforts of suppliers and logistics providers.
And the burden of paperwork, despite moves to a global electronic customs standard, continues to be costly and complex to fulfil, with so many parties involved and varying levels of technology adoption.
A widely adopted blockchain model for supply chain would cut down on much of the paperwork and streamline the verification process.
In my next blog, we’ll examine the benefits, and the pitfalls of blockchain in supply chain. For more information on Cisco’s approach to securely connecting the supply chain, visit our website.
This blog is extracted from an article first printed in The Manufacturer (April 2017)