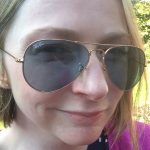
Accelerating Industry 4.0 – 5 Key Priorities for European Manufacturers
3 min read
European manufacturers are experiencing almost unprecedented political, economic and social uncertainty. From Brexit to increasing global tensions and exchange rate volatility, the future is less than clear.
UK Manufacturing, while generally performing well up to now is showing signs of strain. Country Purchasing Managers’ Index (PMI) – a key industry performance indicator – fell to 54.6 in January 2017, below market expectations. While slipping further from the record high of 61.50 achieved in January 2011, it is still and a safe distance from the record low of 34.40 seen in November 2008 (source: Markit Economics).
To safeguard the long-term competitiveness of our manufacturing and – in turn, our economy, innovation is needed now more than ever. The design principles of Industry 4.0 – interoperability, information transparency, technical assistance and decentralised decisions – provide a comprehensive framework for future-proofing your manufacturing business. Yet the pace and intensity of change can make it difficult to know where to focus investment and resource.
To maintain competitive advantage in the rapidly-changing global landscape, manufacturers must prioritise their efforts in these key areas:
#1 – Smarter machines
Automation alone is no longer enough. Artificial intelligence will soon become commonplace on the plant floor, with sensors routinely deployed to spot defects easily missed by the human eye, but with the potential to create major quality issues down the line and rack up significant costs in repairs, recalls and lost business. Machines will not only perform ever-more sophisticated tasks, but machine learning will drive quality and productivity improvement across industry. Manufacturers operating antiquated networks will be unable to keep pace with the demands of digitisation and must take urgent action to put a flexible, secure industrial network foundation in place.
#2– Smarter people
Manufacturing is going digital, but what about the workforce? The industrial sector is definitely seen as a laggard in terms of mobility and, as a result work-life balance, with many of the talent employers so desperately want to attract and retain frustrated by the need to be in the office or on the plant floor to carry out critical tasks. And, in addition to concerns over the impact of carbon emissions, the introduction of new travel restrictions may set a trend that means global travel is more difficult in the future, so international businesses will need a plan B rather than dispatching employees in person. Collaboration technologies can solve many of these issues, from HD video on the factory floor enabling remote experts to step in to solve issues, to on-demand video conferencing and app-based team spaces that facilitate immediate information sharing.
#3 – Embracing new and emerging technologies
AR and VR offer huge potential benefits in the industrial environment. Where multiple sites are the norm and facilities are frequently vast in size, getting to a machine to investigate an alert or carry out routine maintenance is currently a much bigger job than you might expect. It’s still surprisingly common for a critical machine to be out of action while an expert is flown in to diagnose or fix a fault. Mixed reality on the factory floor can enable a local technician to access drawings, manuals or videos to resolve an issue or even share live video and be guided to fix a problem by a remote expert on another continent.
#4 – Collaboration through the value chain
The industrial internet of things (IIoT) works on the basis that all things can connect easily. Yet the manufacturing environment is full of connectivity and communication protocols that are not interconnected and often not interoperable. Convergence and interoperability in the form of industry standards are critical if Industry 4.0 is to live up to expectations. A group of leading industrial technology vendors, including Cisco, General Electric, National Instruments & Schneider Electric, committing to developing products using the same communications protocol. Collaboration between links in the value chain, including competitors is necessary to realise the potential of digitisation.
#5 – Security
Manufacturing is now one of the top three industries targeted in cyber-espionage and the number of attacks on legacy industrial control systems has also sharply increased as they are increasingly connected to corporate networks and the internet. Manufacturers must get serious about security ahead of regulatory changes which will force industrial businesses to disclose cyber-attacks, even where no customer data has been compromised.
To see how Cisco is working with manufacturers to support these priorities, visit us at Hannover Messe 24-29 April (Hall 8, stand 13) or visit our website.